An Eco House Constructed in Just Four Days
Believed to be the first of its kind in the British Isles, this semi-detached housing project took just four days to construct.
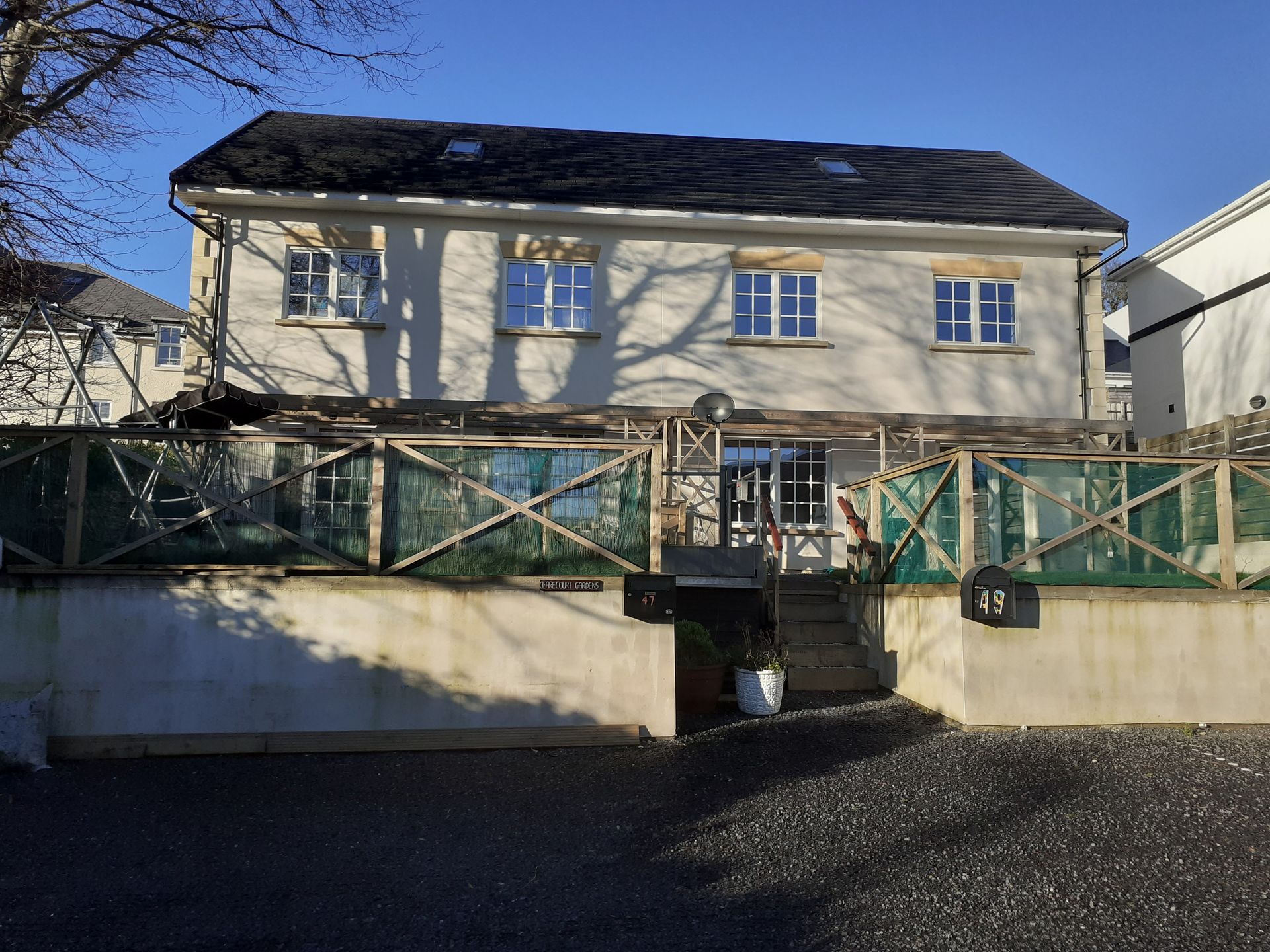
In Douglas, on the Isle of Man, our customer John Sheppard recently completed a pilot project in his effort to develop a ‘whole house package’ for easy passivhaus building. Believed to be the first of its kind in the British Isles, this semi-detached housing project took just four days to construct.
John has been working with the Swedish architect Hans Eek who co-founded the Passive House movement since 2003 to identify a series of components readily available in the British market that would allow them to construct a house for the social and affordable sector of the construction market in as little as eight weeks.
According to John, finding the right foundation system was their biggest challenge but after discovering that ISOQUICK was available in the UK from Build Homes Better, it became their chosen foundation system.
As for the other components, in keeping with their aim to make the project as sustainable as possible, they used the Decra metal roofing system, cladding the exterior of the frame with Savolit Plus wood wool slab and then rendered with K Lime to give it a fully breathing structure. They also had to design their own continuous cavity weep vent using 0.5mm 316 stainless to enable the fully breathable cladding to work to its full potential.
Permeable paving and a tree root protection system from the ABG were used to contain all rainwater within the site and protect the tree roots from the adjacent mature trees which being deciduous were also used to improve summer shading and cooling.
Reflecting on the ISOQUICK install, John said:
“Luckily we managed to install the ISOQUICK foundation system in the late summer of 2019. Myself and my resident engineer installed the slab together with the concrete reinforcement within a single week.
After that, our val-u-therm hybrid timber frame was delayed as the Scotframe erection team were running late. But thankfully, both units were erected within a four-day break in the weather towards the end of 2019.
Completion of the project was anticipated to be achieved by early Summer 2020 however the Covid pandemic and lockdown meant the units weren't fully completed until the end of 2021 with myself carrying out much of the internal and external fit out due to the restrictions imposed. Individual specialist trades also came in to complete their works in accordance with lockdown regulations.”
John is pleased to have completed the project within existing social and affordable housing budgets, proving that the concept could provide the British housing market with a sustainable affordable construction format.
“The fact that weather tight status could be achieved within a matter of days rather than the weeks or months of more traditional build formats allowed internal fit out to commence immediately with external completion achieved as weather conditions allowed, significantly speeding up the build process.
We have now been living in the left-hand unit since February 2022, maintaining an internal temperature of circa 24 degrees centigrade throughout with no additional heating required apart from solar gain and the otherwise waste heat from us and our appliances.
In December 2022, the outside temperature fell to -5 degrees centigrade and to maintain the internal temperature we used 1kw of off-peak heating from midnight to 6am in the morning to prevent the internal temperature falling below 20 degrees centigrade.
Aside from that, we haven’t had the heating on since February 2022.”
John told us that since completing the project, interest from local developers and private clients has increased but many are still nervous about using a build format with which they are not familiar. He hopes that this will change in the coming years as the need for energy efficient homes becomes even more critical.
Discover more about this project. Watch the Isle of Man TV interview with Paul Moulton, the local architect working on the project below:
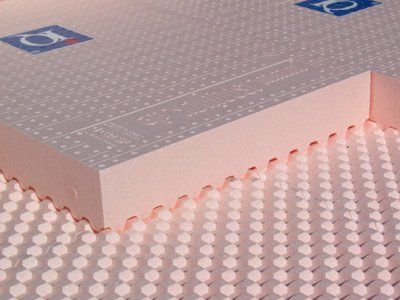
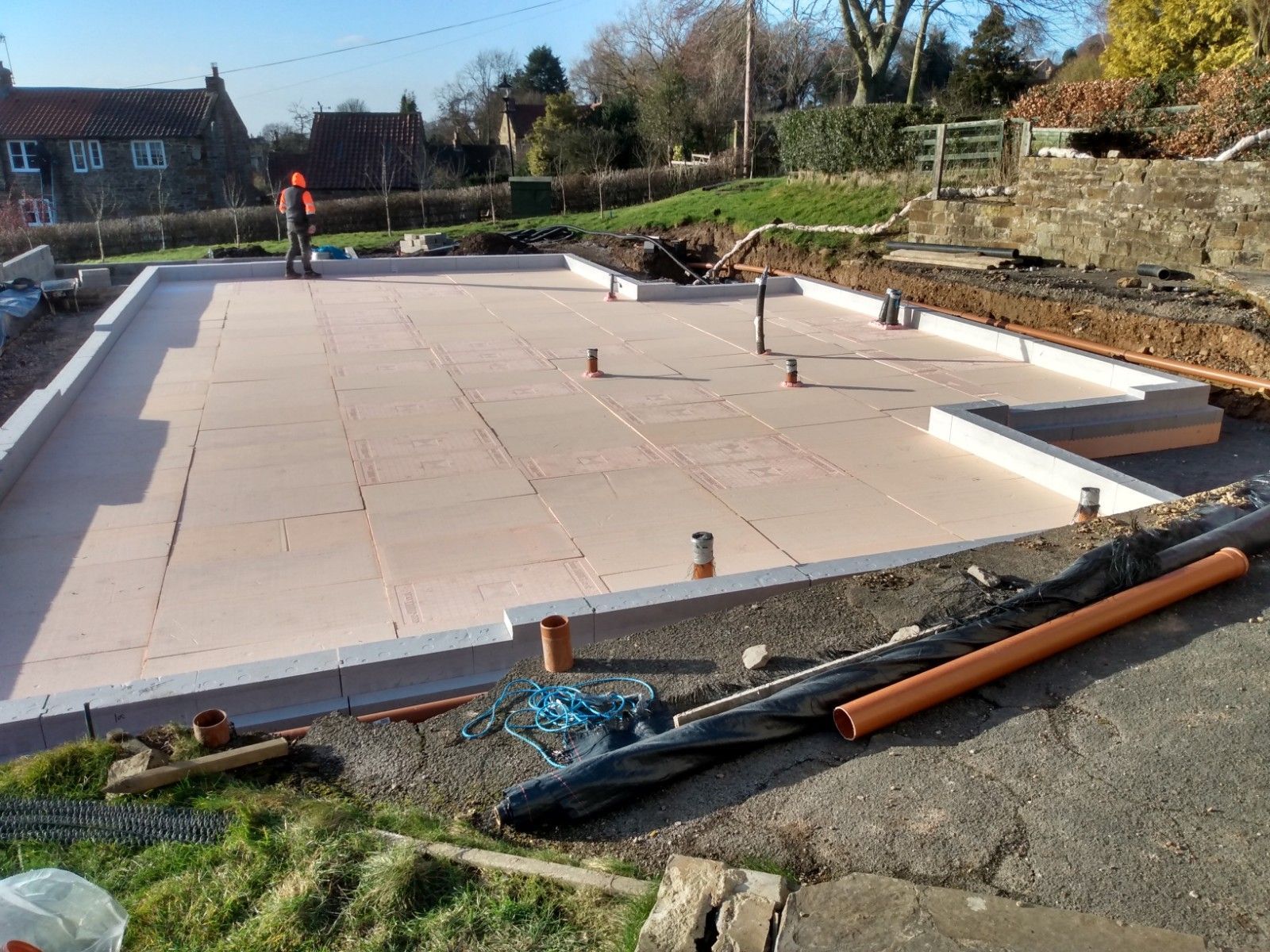
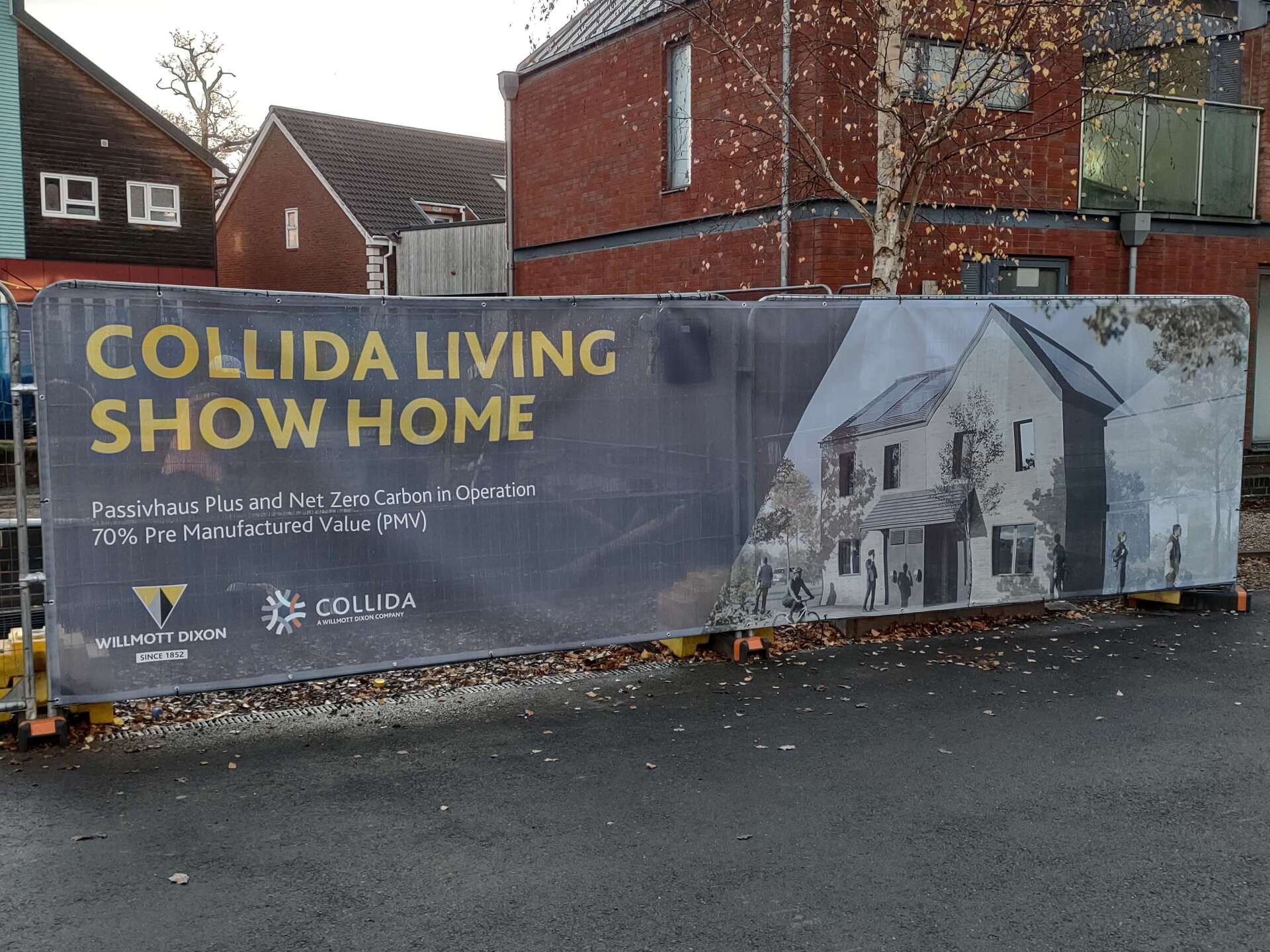